Process Safety in Motion
DKC’s approach to improving Process Safety
Ensuring safety in chemical, pharmaceutical, and most other industrial operations is crucial due to inherent hazards such as handling flammable materials, high pressures, and corrosive or toxic substances. The management of these risks falls under “Process Safety Management” (PSM). Regulations like the European Seveso III Directive and the American OSHA PSM Standard primarily focus on large-scale operations that impact the public beyond their facilities, thereby excluding smaller operations and the process safety of on-site personnel from their scope. At DKC we know that process safety is equally important for “non-seveso” operations.
To enhance Process Safety performance, De Kort Consultancy introduces “Process Safety In Motion,” (PSIM) a program designed to assist clients with implementing and optimising PSM. We used a Risk-Based approach to prioritise the process safety elements to implement or to improve. DKC offers practical support in setting up the systems and procedures to achieve swift and tangible improvements in Process Safety. When needed we will also train staff in understanding and living PSIM.
The term “In Motion” underscores the dynamic nature of activities during implementation and the continual commitment to prioritising Process Safety in day-to-day operations.
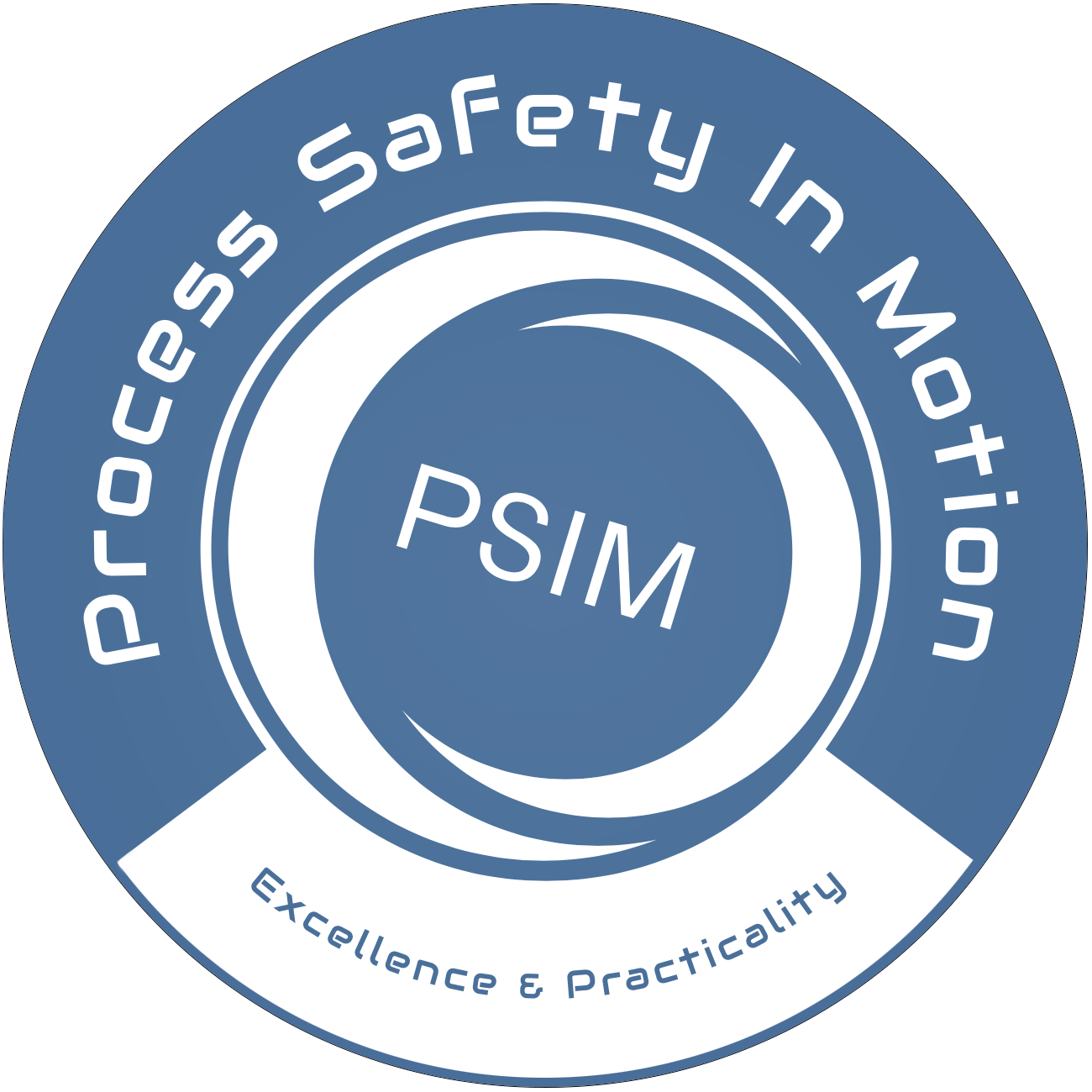
Our services
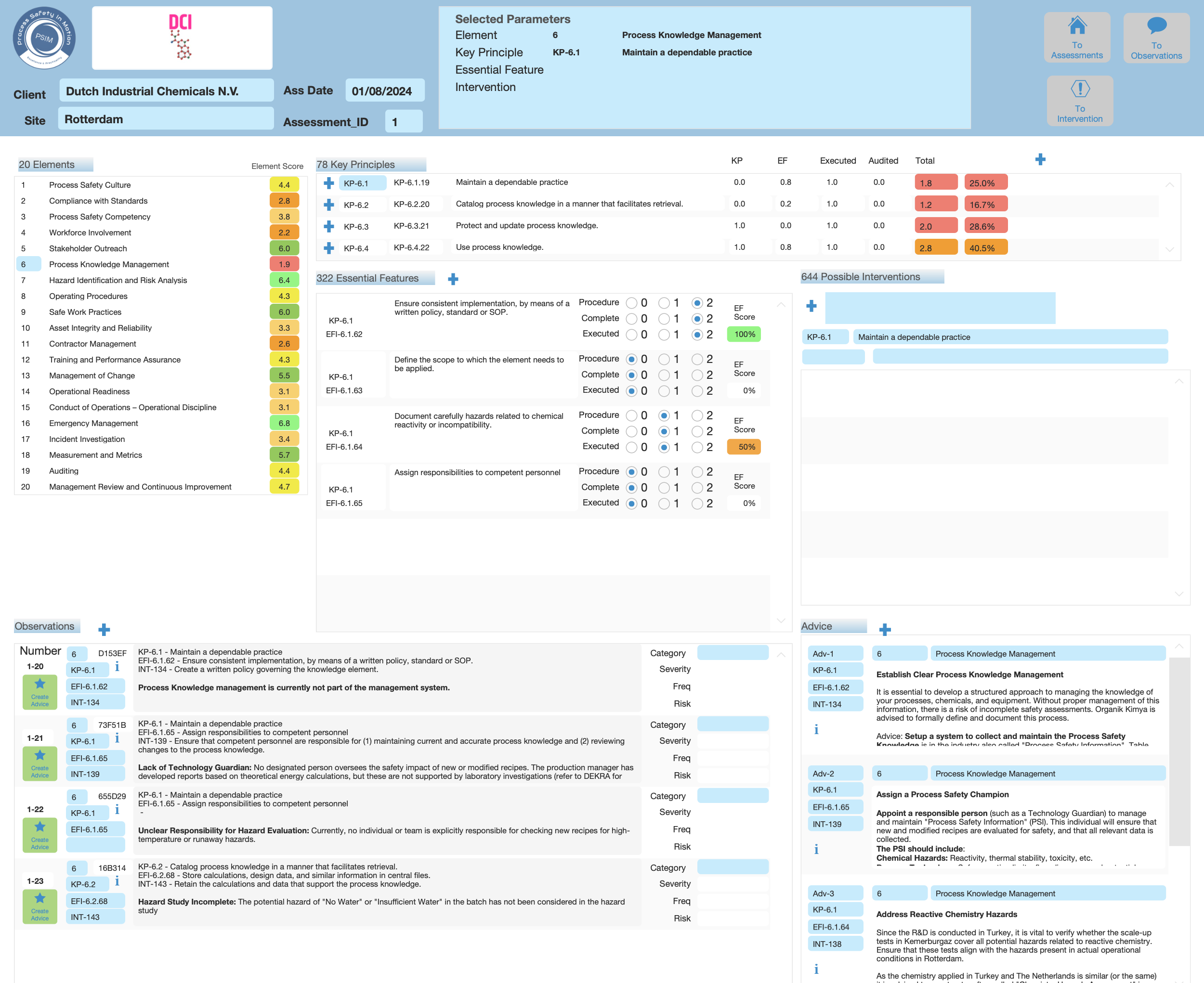
Process Safety Performance and Culture Assessment
DKC has used developed a method to assess the performance and culture of Process Safety during a well prepared PSIM assessment. During a multi-day visit all 20 elements of the CCPS Risk Based Process Safety system will be assessed, prioritised. Subsequently we select 3 to 5 elements where improvements are most effective to reduce the Process Safety Risk of the location. Per selected element we prepare 3 to 5 tangible and practical recommendations for improvements,
The client will use the recommendations in their Process Safety plans and implement these within 3 to 12 months. If needed DKC will support the implementation to achieve maximum momentum for improvements.
Therefor the PSIM assessment goes over en beyond an audit.
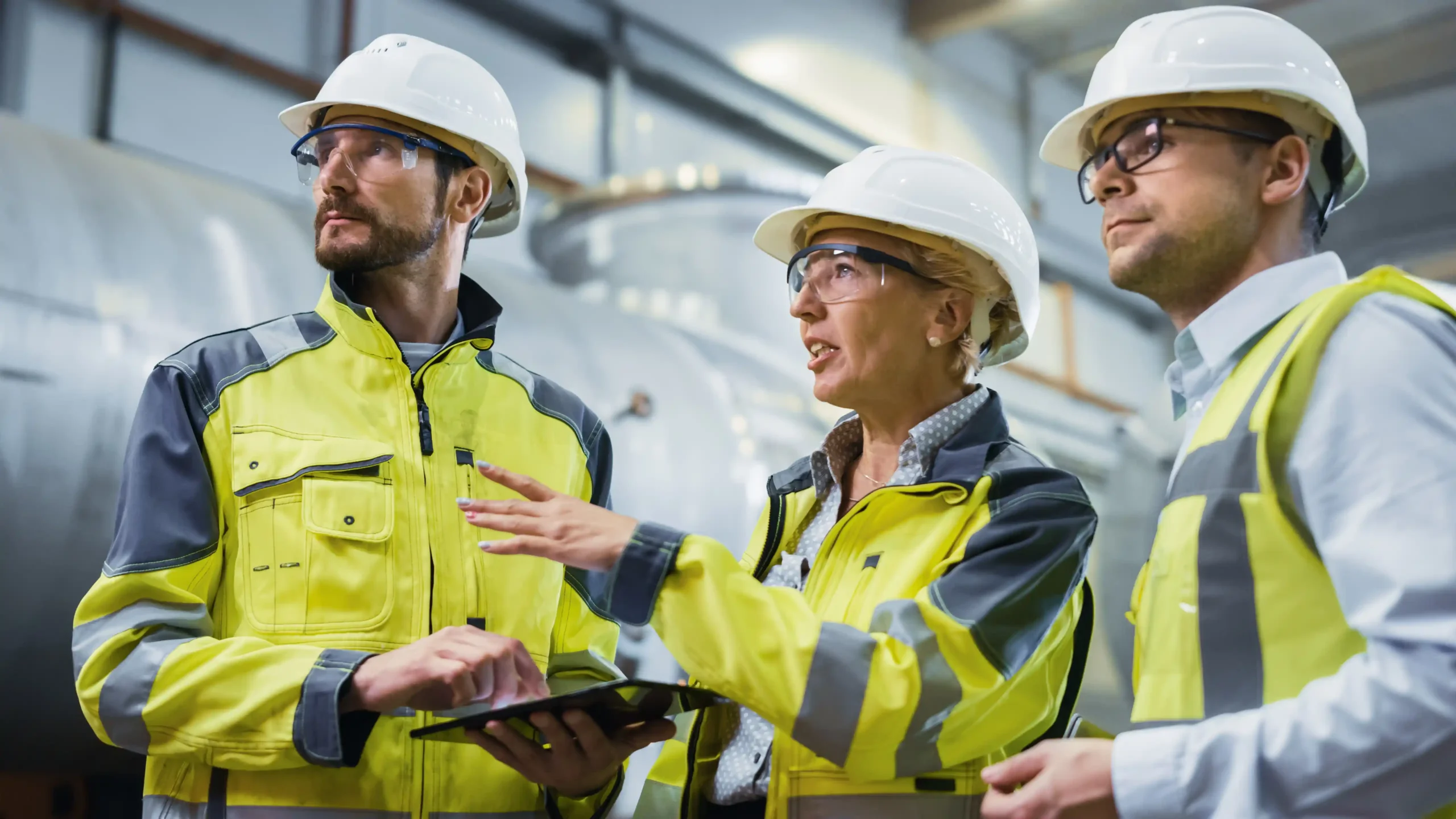
PSM Implementation
When it comes to implement Process Safety management systems DKC has ample experience to do so in a Practical manner. We can advise on which elements of the 20 PSM elements to implement or improve to reduce Process Safety Risks and gain maximum Performcane increase.
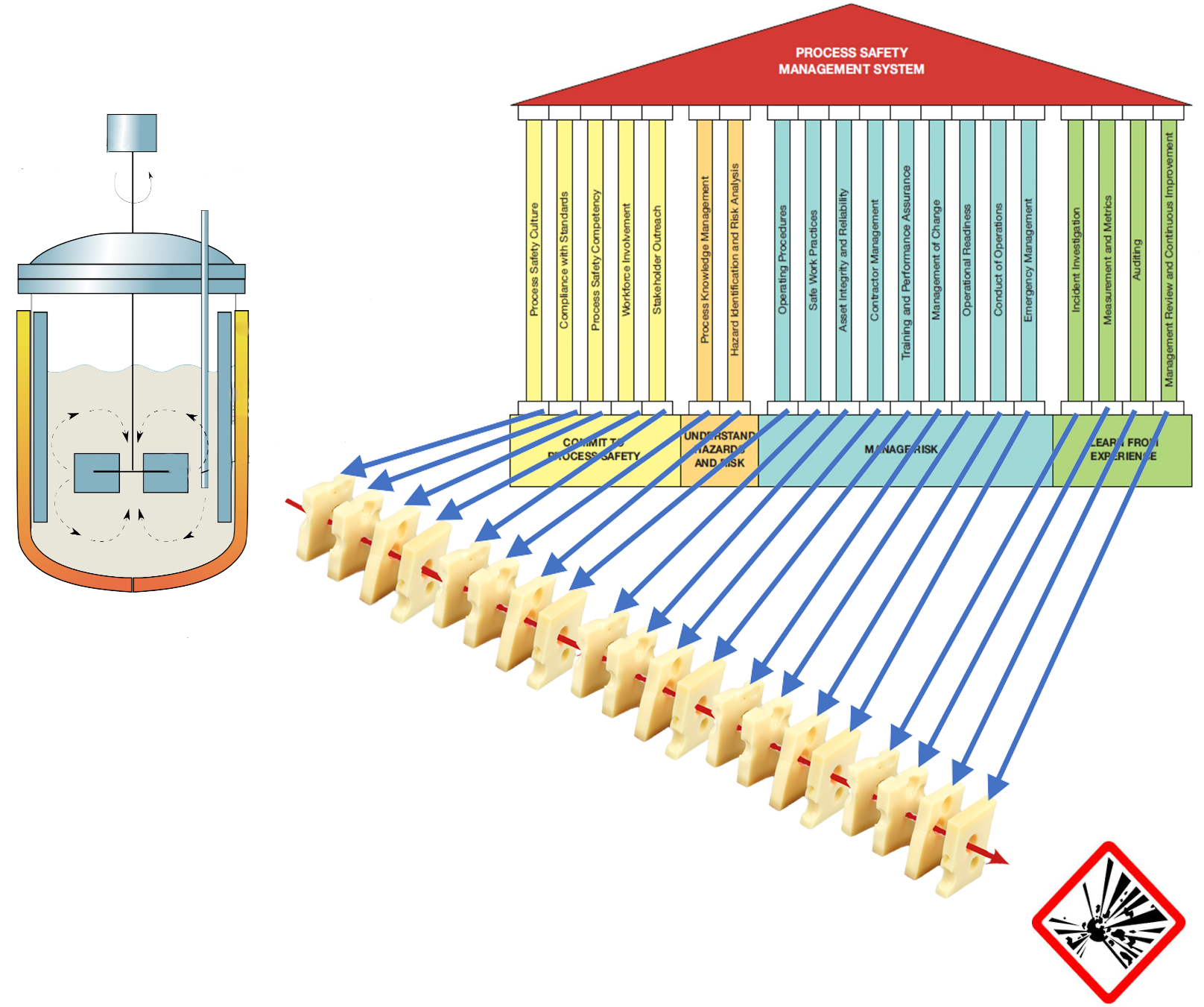
Pioneering Compliance Solutions for Hydrogen-Powered Public Transportation to PGS 35 & PGS 36
At DKC, we have developed a comprehensive audit protocol designed to assist a public transportation company in complying with Dutch regulations for hydrogen-powered, zero CO₂ emission buses. Our protocol strictly adheres to national standards, PGS 35 and PGS 36 guidelines, ensuring the highest levels of safety and regulatory compliance.
Successfully implemented with a major bus operator that runs hydrogen-powered buses and hosts an on-site hydrogen fueling station owned by their hydrogen supplier, our tool highlights compliance challenges presented. By accommodating scenarios where fueling infrastructure is owned by a third party but located on the operator’s premises, we, our protocol streamlines compliance processes and promotes efficient operation of hydrogen bus fleets.
Partner with DKC to confidently navigate the complexities of hydrogen technology and regulations, contributing to a sustainable and environmentally friendly future.

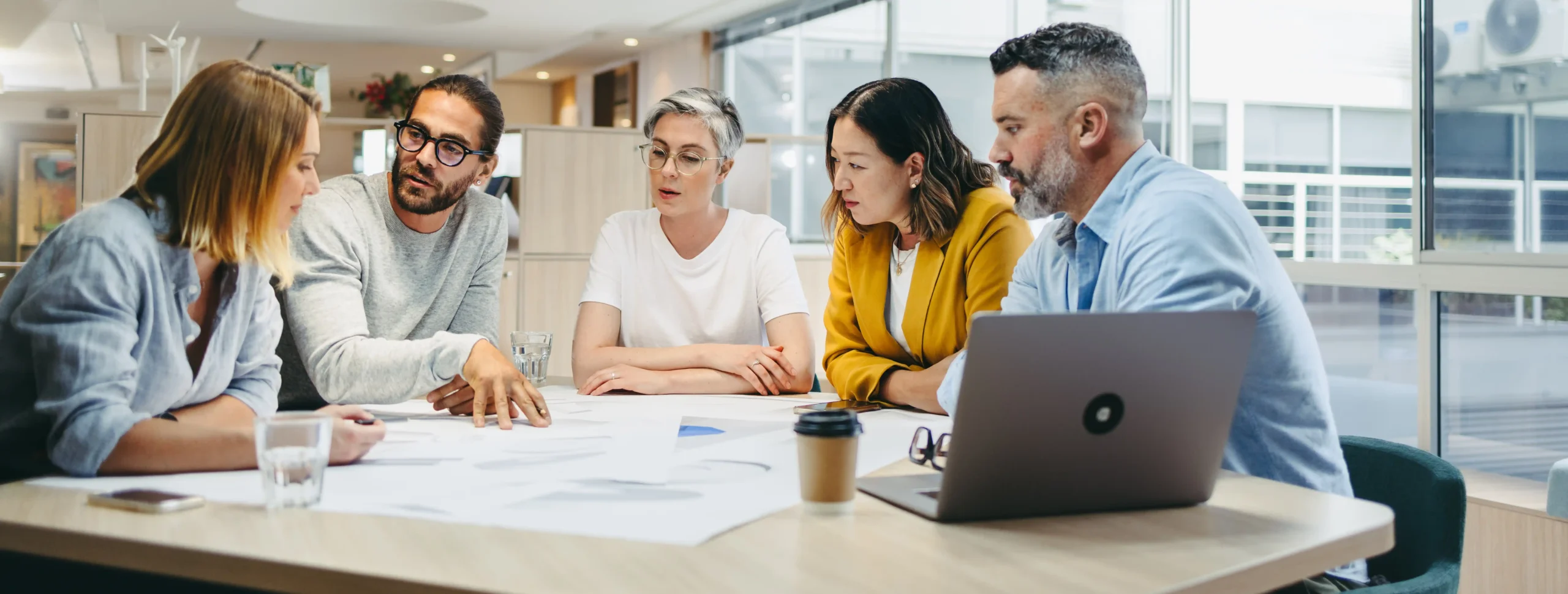
Risk Asssessment
Risk Assessments are the corner stones of the Process Safety Management system. Multiple types of Risk Assessments are used in the industry, such as HAZOP, LOPA, FMEA, QRA, JSA, What-If, HAZID, Bow-Tie etc.
All of them have their own Pros and Cons. DKC helps its clients to select the right technique and is also capable of leading / assisting them during the selected studies, using the leading pieces of software tools such as PHA Pro and PHA Works.
Smart Allocation
Once the risk assessment is completed the creative part of the safety engineering starts. Safety recommendations traditionally often result in adding more and more safety equipment, procedures or instrumentation to an installation. DKC has developed a method to define the “Best Solutions” involving a multi-disciplinary design session following a defined process, which is called “Smart Allocation”. Where defining the “Best Solutions” is using criteria, like is it easy to build, use and maintain, is providing the level of safety improvements needed and is is economically attractive? Hereby DKC uses the philosophy of Inherently Safe(r) Designs.
Experience has shown that “Smart Allocation” can save 30 to 90% of the investement cost, while still obtaining all the improvement needed.
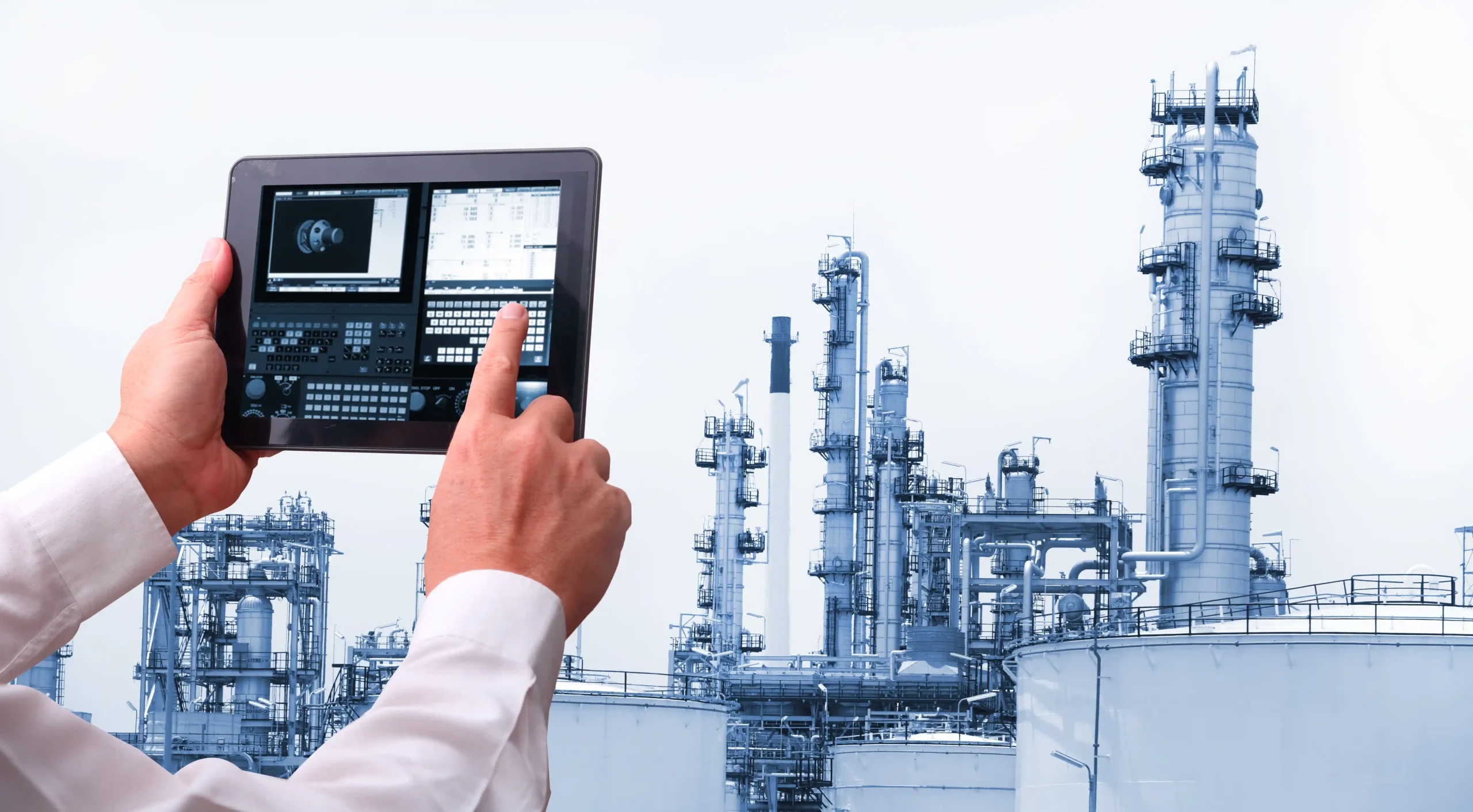
Improve your safety program today.
Just starting out?
If you are just getting started and need help developing a safety program, DKC can guide you through the process.